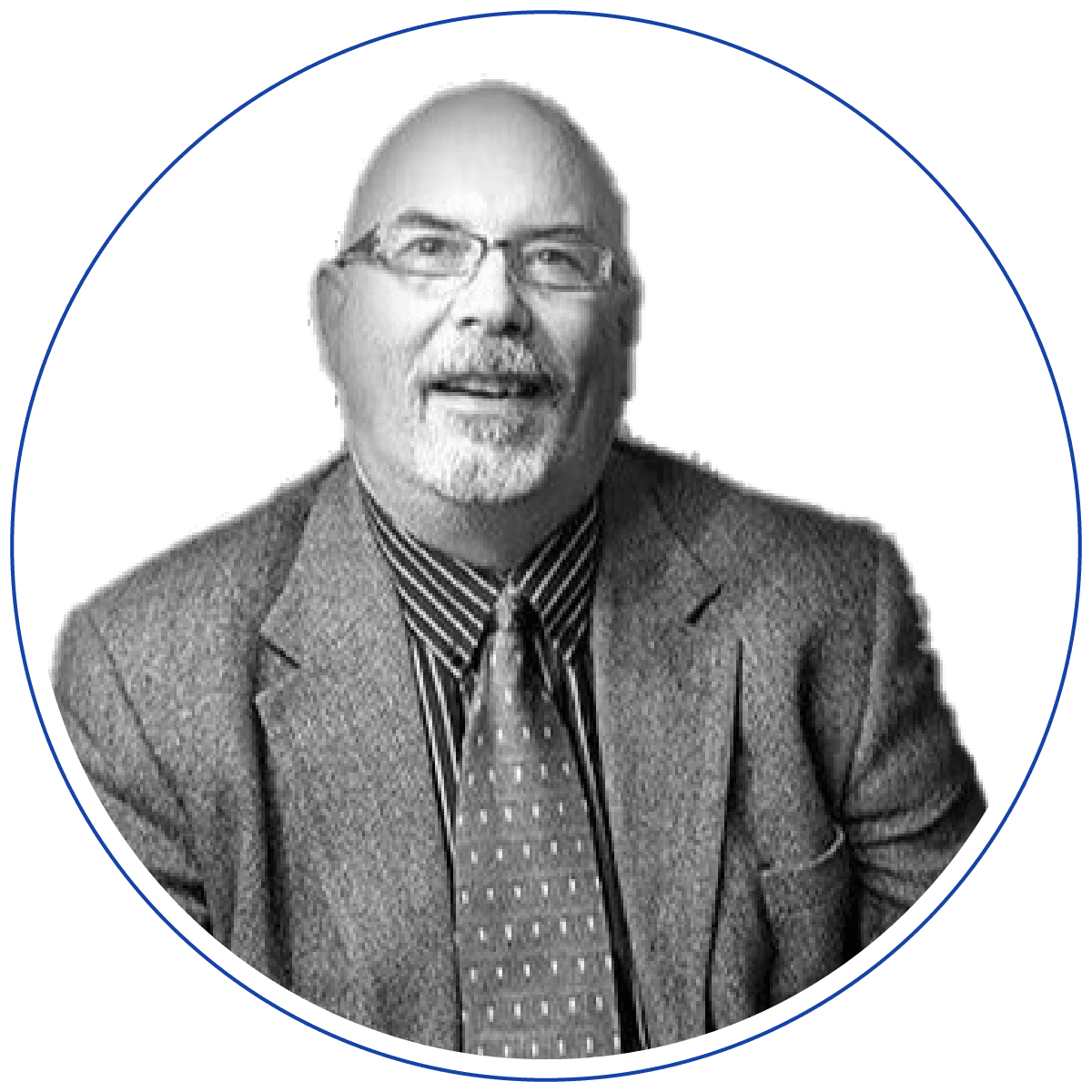
This article is written by
Andy Pratico
More Equipment manufacturers are looking to extend their ERP capabilities. Engineer-to-order and project-based manufacturing systems, have always been essential for equipment manufacturers. Today, equipment manufacturers are recognizing the value of integrated Quality Systems to address and comply with International Organization for Standardization (ISO) standards. Additionally, integrated Service Management is becoming a critical for equipment manufacturers.
Integrated Quality Within Your ERP is Expected
Quality control is crticial for equipment manufacturers. Equipment need to be tested and inspected, ultimately capturing the data in a system of record. Equipment manufacturers need these records to prove compliance with ISO standards. Having a native Quality Control System as part of their ERP will solve these quality control demands.
Integrated ERP quality control systems are used for inspecting parts, in-process inspections, and final acceptance testing. They can also manage non-conformance, corrective actions, as well as Documents that are tracked and viewed as part of the system.
Infor Quality Control Benefits
Value achieved...
- Incorporate quality process controls across organization
- Track quality info on incoming, in-process and outbound material
- Manage non-conformance and corrective actions
- Manage equipment calibrations and inspections
- Track quality activities, actions and topics key to continuous improvement
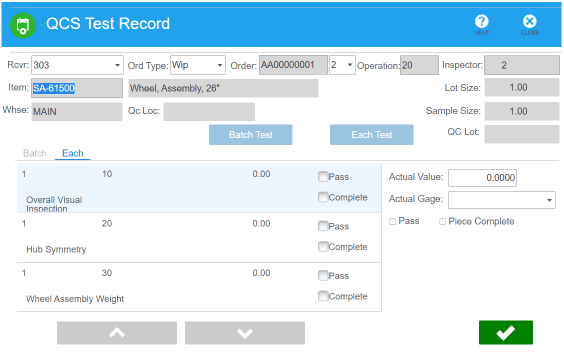
Using smart devices Infor’s data collection system provides for quality inspections on the shop floor.
Integrated Depot and Field Service Management
Service - Installation and Delivery
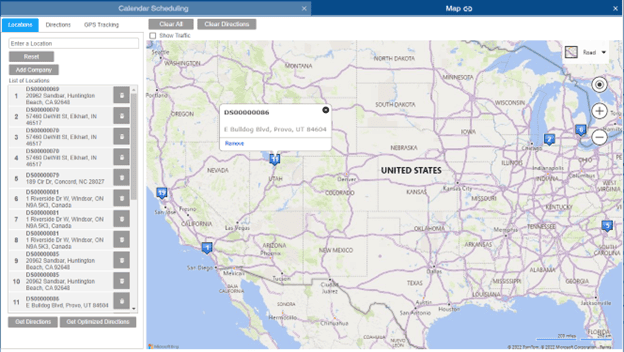
The prep, transport, and set-up costs are also captured as part of the project, enabling the manufacturer to measure and analyze true profitability.
An ERP with integrated service management should accommodate these requirements, as well as equipment rentals to delivery scheduling and more.
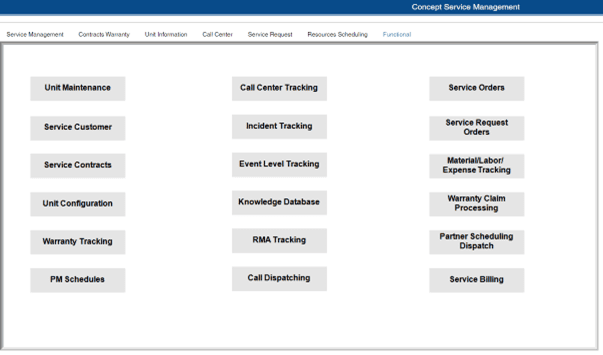
Infor ERP provides equipment manufacturers with robust tools to manage service activities, from installation to maintenance.
Service Management - Warranty and Service
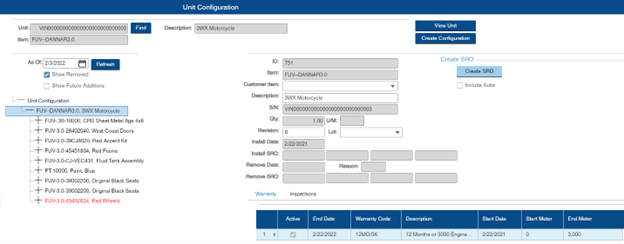
Infor ERP’s integrated Service Management provides visibility into unit configuration and current configuration from previous repair and warranty work.
Infor’s service management facilitates the ability to take photos, obtain electronic customer sign off, and recording labor and materials used on the service repair order. These costs can be attributed to the warranty, or against a service contract, or be billed to the customer for repairs. Due to accounting integration the billing happens instantaneously, increasing cash flow and fewer days outstanding for the service department work.
Summary
The benefits of having an end-to-end equipment manufacturing ERP system are numerous. However there are few ERP options available that address these diverse functional needs, such as integrated quality control and service management. Most ERPs recommend 3rd party bolt ons or ISVs (which are never as integrated as a single end-to-end system).
Infor ERP is a unicorn, that offers end-to-end integrated functionality and never imposes 3rd party bolt ons.