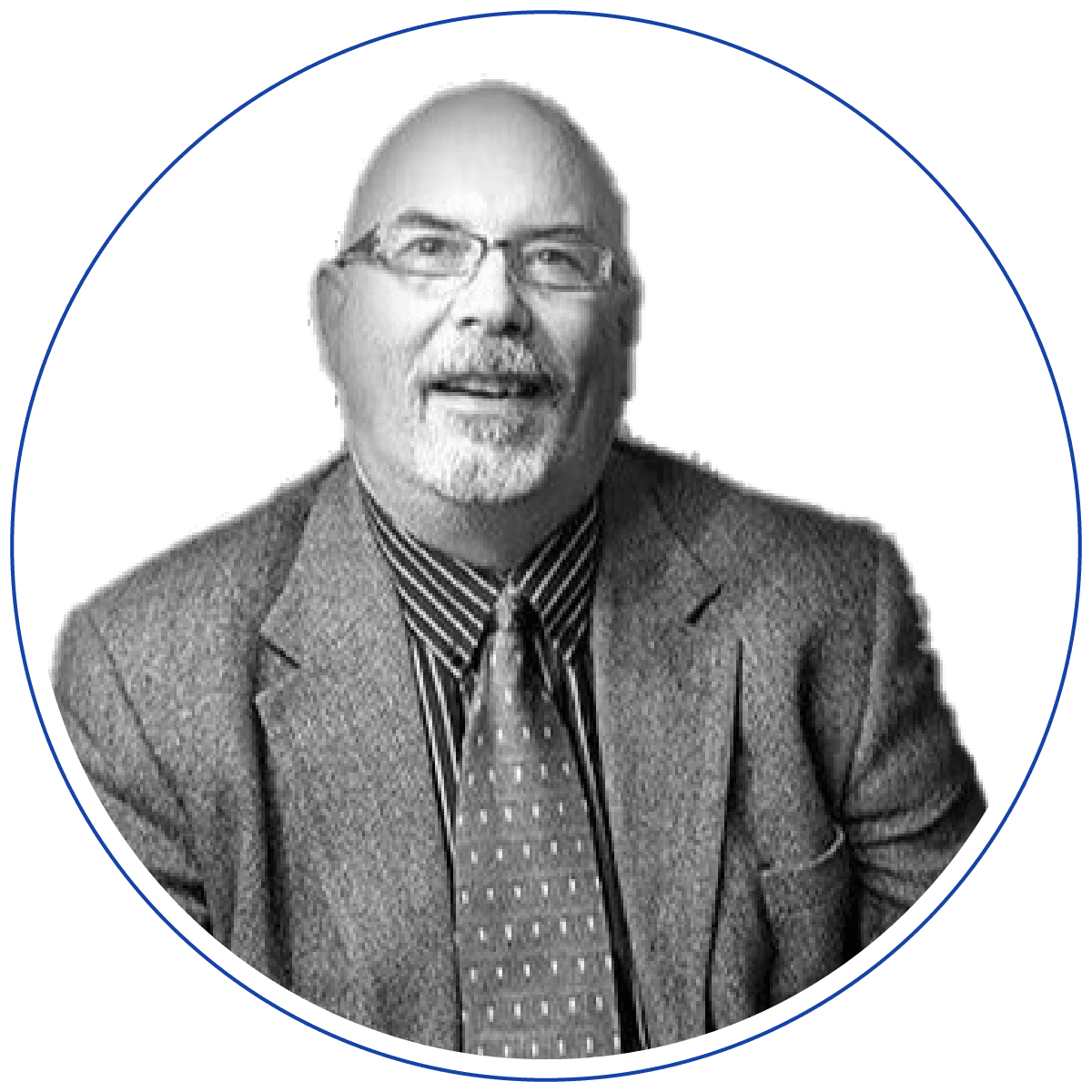
This article is written by
Andy Pratico
What does ETO mean?
“Project-based or ETO (engineer-to-order) is commonly used to describe a custom manufacturing process, yet is rarely described with real world differentiation. Few MES (Manufacturing Execution Systems) solutions are specifically focused on meeting the needs of this challenging manufacturing market. Estimating costs to maintain a decent margin is often one of the great complexities in the ETO environment. Project-based cabinet makers, for example, may have never built a one-of-a-kind item before or have to add items once they are on the production floor, and have to accurately guess all the possible costs variations.” - T.R. Cutler, Information, Information, Information (Business Excellence Magazine, Sept. 2007)
ETO Manufacturing Challenges
The ETO manufacturer is faced with maintaining a business model that demands skilled, experienced, and expensive Engineers who design innovative solutions to very complex problems.
Unlike their repetitive manufacturing siblings, in ETO environments the customer is heavily involved throughout the design and manufacturing process. Bottlenecks in the process include frequent engineering changes and long lead times from purchasing vendors that span months and years. Raw materials are not purchased to stock. Instead, are purchased direct to a specific phase of the overall project. As ETO manufacturers treat each job as a project, all costs and materials are issued at actual and with detailed breakdown comparisons to the original estimate. Once a phase is complete, it is shipped to and assembled at the client’s site. As well aftermarket services and replacement part sales are needed throughout the life of the product.
ETO Manufacturers Requirements
- Engineering Change Management: Implementing authorization levels for approvals and securing material transactions to prevent the purchase or consumption of obsolete items due to an engineering change.
- Preventative Maintenance, Reactive Service and Warranty Agreements: Management of internal equipment maintenance and external aftermarket warranty contracts and repair (depot and field).
- Quoting and Estimating: Including complex product configuration and customer relationship management (CRM).
- Long Lead Time Material Planning: Improving processes that allow early purchasing of items and assigning them to appropriate jobs as the project structure develops.
- Project Reporting: Detailed reporting of actual costs throughout the project lifecycle and tracking time and attendance.
- Project Inventory Management: Aligning inventory directly to projects, particularly for those requiring government project costing and tracking, including the ability to purchase inventory with project funds and track their usage across orders within the project.
- Revision Control: Integrated revision control for engineering BOMs and drawings.
- Quality Assurance: Integrating QA, purchasing, manufacturing, and inventory management, with alerts for non-conforming material (NCR) identification.
- BOM Integration with CAD and PLM Systems: The ability to link ERP’s to BOMs within popular CAD and PLM systems.
- Shop Scheduling Systems: Systems that incorporate task and project time estimates and schedules, rather than being solely date driven.
- Material Planning and Scheduling: Managing materials and schedules at both the project level and the work order level, including coordination with external sub-contractors.
- Configuration Management separating As Designed; As Estimated; As Built; As Delivered; As Maintained: Knowing the exact BOM/Routing structure throughout the finished product’s life cycle.