Digital Operations Platform Deliver Better Outcomes - Essential Software Solutions
Modern business systems and technology have moved from the top floor to the shop floor in many industries. In order to survive and compete in the modern world, more and more companies realize that Digital Transformation and the modernization of business processes are critical. At ESS we help our customers achieve their business goals with a focus on technology, automation, and metrics.
Free Infogrfaphic - Mythbusting the Agile ERP
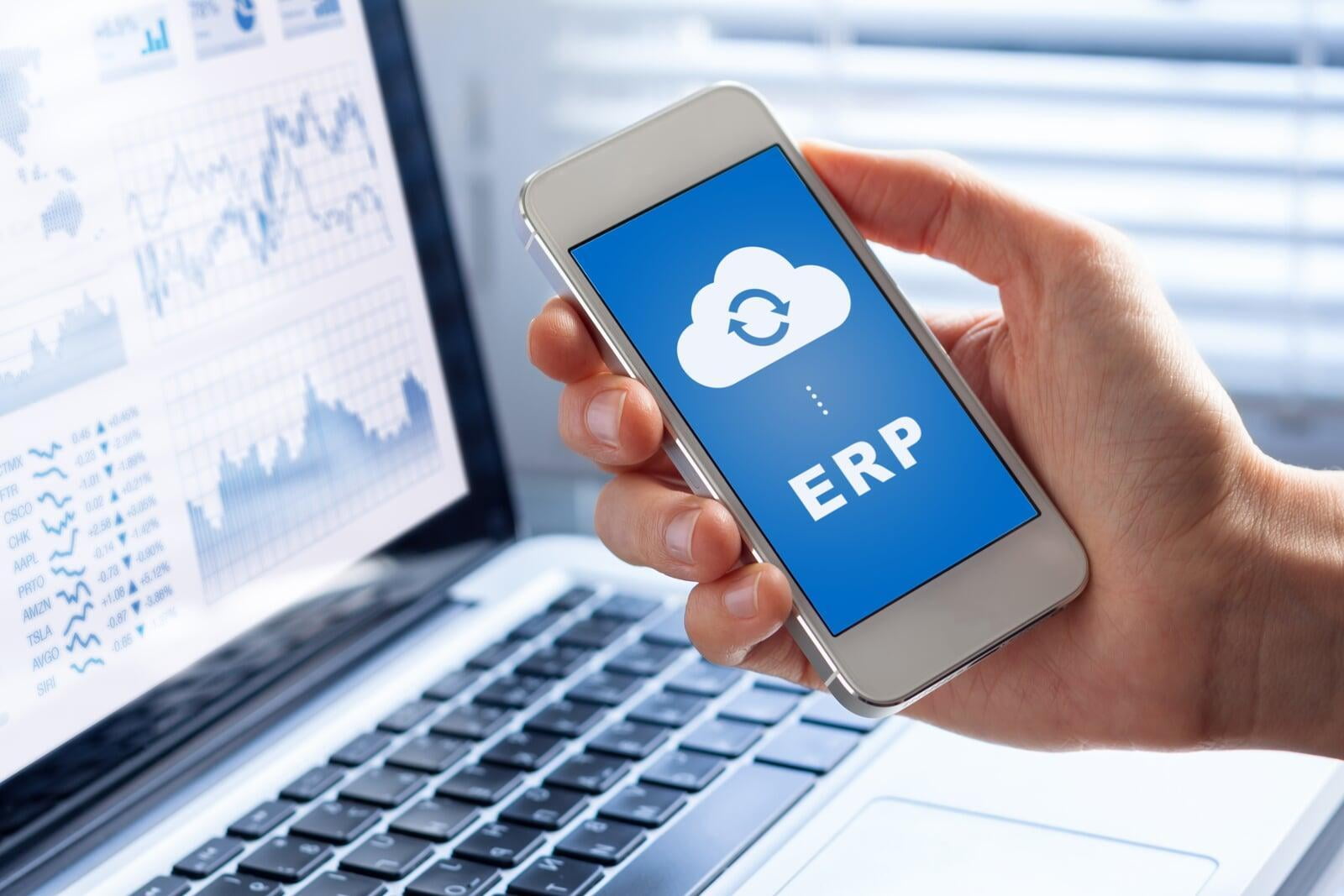
Improve Business Productivity and Agility with modern ERP
A peep at some distant orb has power to raise and purify our thoughts like a strain of sacred music, or a noble picture, or a passage from the grander poets. It always does one good.
Businesses everywhere know they need to stay current to stay relevant. Listen to industry experts...
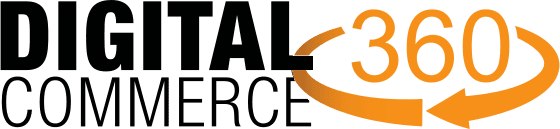
Digital Commerce 360
Xometry takes off as an on demand manufacturing marketplace
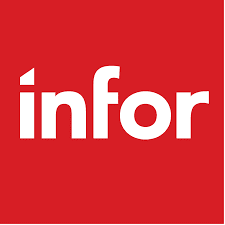
Infor
Gilberts Airs Make to Order Production Benefits with Infor.
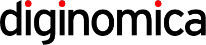
Diginomica
Survive the roller coaster of digitalization with flexible ERP (December 2019)
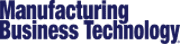
MBT
Two Tier ERP Solutions Help Meet Vertical Industry Needs